Hydrogen-based transformation of the steel industry - Technology and challenges of CO2 neutral steelmaking
Seminar’s Target
Europe wants to become climate-neutral by 2050 and already save 55% of greenhouse gases by 2030 compared to 1990. The EU Climate Act sets these targets in law for the first time. For large parts of the European steel industry, these targets mean a far-reaching technological change. The technical solution has been found and is: Replace coal with hydrogen! But how does the new process route work in detail? What are the challenges? In three days, the seminar will provide a technical overview of the biggest technology change in the steel industry for decades.
Technical Chairman
Jochen Schlüter
Organisation / Registration
Steel Academy
Steel Institute VDEh
Mr Peter Schmieding
Sohnstraße 65
40237 Düsseldorf
Fon +49 (0)211 6707-458
training_at_vdeh.de
www.steel-academy.com
Content
- Ways to CO2 neutral steel production
- Technologies of current direct reduction concepts
- Iron ores for hydrogen-based direct reduction
- Reduction technologies of iron ore fines with hydrogen
- Green ironmaking with hydrogen and ammonia
- Hydrogen as a challenging atmosphere for refractories
- Electric arc furnace technology - AC and DC
- EAF and OBF power supply
- Technology of the OBF (Smelter)
- Melting of DRI and HBI in the EAF
- Future importance of steel scrap
- Project SALCOS: Steelmaking route DR - EAF
- Project tkH2Steel: Steelmaking route DR - OBF - Converter
- Slags of CO2 neutral steel production
- Hydrogen production, transport and storage
- Green power production and availability
- Decarbonisation of downstream processes – H2 burner
- A label system for green steel and green lead markets
Iron Ores
Target Groups
- Mining staff
- Blast furnace staff
- Direct reduction staff
- Raw material and purchasing staff
- Supervisors responsible on metallurgy, raw materials, purchasing and energy
Chairman
Dr.-Ing. Hans Bodo Lüngen
Organisation
Steel Academy
Steel Institute VDEh
Mr Peter Schmieding
Sohnstraße 65
40237 Düsseldorf, Germany
Fon +49 211 6707-478
training_at_vdeh.de
www.steel-academy.com
Content
- Types, characteristics and chemical compositions of iron ores
- Resources and deposits of iron ores
- Thermodynamics and kinetic fundamentals of iron ore reduction
- Sintering of iron ores
- Pelletizing of iron ores
- The blast furnace process
- Various blast furnace operation modes round the world
- Iron ores for direct reduction and hydrogen-based reduction
Cokemaking
Target Group
Maintenance and operating staff / Supervisors responsible for decisions on metallurgy, energy, purchasing and environmental protection / Raw material and energy trading and purchasing staff
The seminar places the emphasis on quality of raw materials and on modern processes and methods of coke making. Lectures on iron and steel making, environmental aspects, refractories and by-products round off the programme. Note: Both during lectures and discussions, as well as in the breaks of the seminar, our guidelines on adherence to cartel-law regulations shall be followed.
Cooperation Partner
VDKF – Association of German Cokemaking Experts
Directed by
Peter Liszio, KBS Schwelgern
Viktor Stiskala, thyssenkrupp Steel Europe
Organisation
Steel Academy
Steel Institute VDEh
Peter Schmieding
Sohnstraße 65
40237 Düsseldorf, Germany
Fon +49 211 6707-478
training_at_vdeh.de
www.steel-academy.com
Content
- Production of Iron and Steel
- Blast Furnace Process
- Coal Formation, Mining and Beneficiation
- Coal Quality / Coal Blending
- Coal to Coke Transformation
- Coke Quality
- Coke Oven Machine Management
- Battery Heating
- Coke Quenching
- Coke Oven Life Prolongation
- Refractory Technology – Coke Oven Lining
- Shut Down Principles => Team Work: Shut down your Coking Plant!
- By Product Plant Operation
- Outlook – Future Aspects of Coke Making
- Coking Plant Tour at KBS Schwelgern, Duisburg
Ironmaking
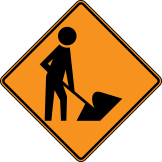
under construction
Oxygen Steelmaking
Target Group
Two thirds of the world's crude steel production runs through the converter. The converter will also take its place in future CO2-neutral steel production in combination with direct reduction and the OBF. In addition to this new future role, the current challenges and trends of the converter will of course also be content of this seminar: scrap qualities, tramp elements, modelling and CFD as well as refractory technology. The programme will be rounded off with the most important fundamentals such as thermodynamics, reaction kinetics and heat and mass balance.
Our target groups are:
• Steel shop operating staff
• Employees in R&D and transformation
Chairmen
Karl-Heinz Spitzer, TU Clausthal
Jochen Schlüter
Organisation
Steel Academy
Steel Institute VDEh
Peter Schmieding
Sohnstraße 65
40237 Düsseldorf, Germany
Fon +49 211 6707-458
training_at_vdeh.de
www.steel-academy.com
Content
- History, developments and types and of oxygen converters
- Thermodynamic and kinetic basics in the converter process
- Tramp elements
- Hot-metal pretreatment
- Computational Fluid Dynamics in the converter
- Design and construction of modern oxygen converters
- Chemical reactions kinetics:
- Refining reactions and slag forming in the BOF process
- Mass balance and heat balance
- Converter process modelling
- Steel scrap for the converter
- Refractory materials for BOF
- Comparison of different converter operation practices: US – Europe – Japan
- Environmental aspects: Dedusting
- Process of CO2 neutral steelmaking
- The role of the converter in CO2 neutral steelmaking
Secondary Metallurgy of Steel
Aim
The aim of this theoretical and practical seminar is to provide participants with an in-depth understanding of the processes involved in secondary metallurgy. Based on special fundamentals, the individual reactors for secondary metallurgical treatment and their tasks will be explained in detail. There will also be an outlook on hydrogen-based green steel production. Discussions and teamwork exercises will round off the range of lectures.
Target Group
Steel shop operating staff / Steel shop maintenance staff / Steel shop installers
Steel shop operation managers / Engineers interested in cleanliness of steel
Chairman
Dr.-Ing. Helmut Lachmund
Organisation
Steel Academy /Steel Institute VDEh
Mr Peter Schmieding
Sohnstraße 65
40237 Düsseldorf, Germany
Fon +49 211 6707-478
training_at_vdeh.de
www.steel-academy.com
Content
- Overview: Tasks of modern secondary metallurgy
- Materials technology’s impact on process metallurgy
- Chemistry crash course: How to read phase diagrams
- Thermodynamic and kinetics for secondary metallurgy
- Fluid dynamics in the ladle
- Kinetics of special reactions in secondary metallurgy
- Deoxidation
- Calcium metallurgy
- Metallurgy of the ladle furnace
- Metallurgy of ladle tank degassing
- Metallurgy of RH degassing
- Metallurgy of VOD and AOD process
- Special melting processes, especially ESR
Electrical Engineering of Arc Furnaces - Power unit for CO2 neutrality
Target Group
The electric arc furnace is taking on a completely new impor-tance in the CO2 neutral, hydrogen-based process routes of steel production and will play a central role. This role also poses new metallurgical challenges. The aim of the seminar is therefore also to highlight these tasks and possible solutions – such as the OBF. However, the focus will be on the electrotechnical fundamentals of the electric arc furnace and the current state of automation technology. Presentations on the supply network, furnace transformers, energy balances and new energy supply concepts round off the programme.
Chairman
Prof. Dr.-Ing. Klaus Krüger
Organisation / Registration
Steel Academy
Steel Institute VDEh
Mr Peter Schmieding
Sohnstraße 65
40237 Düsseldorf, Germany
Tel +49 (0)211 6707-458
training_at_vdeh.de
www.steel-academy.com
Programme
- Importance of the EAF in hydrogen concepts
- Physics of AC and DC arcs
- Design of the AC high-current system
- Equivalent circuit diagram of AC-EAF & OBF
- Short circuit and operating reactance
- Design of the AC high-current system
- Power supply for EAF and requirements for the supply network
- Excursus: New energy supply concepts for the EAF
- Furnace transformers
- Circle and furnace power diagram of AC-EAF
- Electrical layout of AC Furnaces
- Melting of DRI and HBI in the EAF
- Design and electrical system of the OBF (Smelter)
- Comparison of CO2 neutral routes: DR - EAF versus DR - OBF - Converter
- Closed loop power control of AC-furnaces
- Electric principles of DC-furnaces
- Energy balance of the EA
- Comparison EAF – OBF/Smelter
Refractory Technology: Refractory Materials and Slags in Metallurgy
Target Group
Maintenance and operating personnel, supervisors responsible for plant and unit operations, and managers responsible for decisions on refractory problems will learn about new materials and installation methods.
Directed by
Dr. Patrick Tassot,
Dr.-Ing. Helmut Lachmund
Organisation / Registration
Steel Academy
Steel Institute VDEh
Sohnstraße 65
40237 Düsseldorf, Germany
Tel +49 211 6707-454
training_at_vdeh.de
www.steel-academy.com
Content
- Basics on chemical and mineralogical composition of refractory material and slag
- Testing and evaluation of refractory materials in the laboratory
- Synthetic alumina raw material and high alumina cement
- Insulating materials for the steel industry
- The world of monolithics
- Machines for processing and delivering refractory concretes and sprayable refractories
- Basic bricks for the steel industry
- Production and Use of Blast Furnace Slags and Steel Slags
- Blast furnace slag and refractory material
- Converter slag and refractory material in the oxygen blowing process
- Ladle slag and refractory material in secondary metallurgy
- Limestone minerals, lime and dolime and their use in the Iron and Steelmaking
Refractory Technology: Applications, Wear Mechanism and Failures
Target Group
Maintenance and operating personnel, supervisors responsible for plant and unit operations, and managers responsible for decisions on refractory problems will learn about new materials and installation methods. Refractory installers, third party inspectors and contract maintenance personnel will particularly benefit from detailed discussions on new installation techniques and refractory materials.
Directed by
Dr. Andreas Buhr, Frankfurt
Organisation
Stahlinstitut VDEh
Stahl-Akademie
Sohnstraße 65
40237 Düsseldorf
Fon +49 (0)211 6707-458
training_at_vdeh.de
www.stahl-akademie.de
Content
- Steel manufacturing process
- General overview of wear mechanisms and methods for examination of the refractory material after use
- Refractory lining and wear mechanism of blast furnace, taphole, and runners
- Refractory materials for direct reduction plants
- Process conditions affecting the refractory lining life and the development of refractory materials technology in oxygen blowing converters
- Steel Teeming Ladle: ladle metallurgical treatment, refractory stress, materials and lining concepts
- Refractory lining and wear of AC and DC furnaces
- Economics in refractory usage
- Challenges and solutions for continuous casting refractories in consideration of clean steel, automation and economy
- Teamwork on failure case studies
Steel Ladle Lining: Refractory concepts for a complex reactor
Target Group
The wear of refractory materials in the secondary metallurgy is particularly high. These high wear mechanisms are complex, but mainly caused by slags. High temperatures, long-terming treatment and turbulences of stirring gas are also important factors for wear and failures.
Maintenance and operating personnel, supervisors responsible for plant and unit operations, and managers responsible for decisions on refractory problems will learn about new materials and installation methods.
Directed by
Dr. Andreas Buhr
Dr. Helmut Lachmund
Organisation
Steel Academy
Steel Institute VDEh
Sohnstraße 65
40237 Düsseldorf, Germany
Fon +49 211 6707-478
training_at_vdeh.de
www.steel-academy.com
Content
- Trends in clean steel technology and steel ladle lining
- Demands on refractories for secondary metallurgy
- Improvements of the steel ladle linings
- Refractory lining for varying operating conditions
- Improvement of lining for a 400 mt steel ladle
- Thermal efficiency of teeming ladles
- Steel ladle lining for flat steel production
- Monolithic lining in a 3-converter-shop
- Purging plugs in steel ladles
- Exercise: Optimization of economics in refractories
- Teamwork: The digitalized steel ladle
- Steel plant and refractory tour