Plant Management
Plant Management
Plant management in the steel industry
Classic considerations of steel production divide the integrated metallurgical plant into the stages of ore preparation followed by coke, pig iron and steel production, followed by forming (rolling, forging, pressing) and surface treatment (coating) or further processing. Mastering such systems and maintaining the high value of the plant involved requires organisational and tactical units that are consolidated in the companies of the steel industry under the terms ‘plant engineering’ or ‘plant management’. Plant management consists of all the measures undertaken to ensure the efficient, quality-oriented and safe operation of steel production plants.
Many innovative technical developments during the last 25 years, in particular, have allowed cost-effective production, greater flexibility, constant improvements in quality, and the development of new products. The current high technical level of development also continues to ensure the competitiveness of the European steel industry.
Efficient plant management enables cost reductions
Despite its many individual processes, steel production is a closed complex, i.e. a system of individual plants that are networked with one another via logistical and IT connections. The current high state-of-the-art in areas such as automation technology, sensor systems and hydraulics is the prerequisite for being able to operate many of the increasingly complex production plants. The need for optimised plant operating costs is rising given the ever-increasing competition and capital market pressure. Whereby it is the maintenance costs that are often the subject of attention. These represent a not insignificant proportion of plant costs (for construction and operation). A comprehensive optimisation of investment and maintenance management through a holistic consideration of costs – from the new construction, through the entire service life, to replacement – opens up further cost-reduction potentials.
The development and construction of plants
Implementation of an investment in the steel industry is divided into a range of complex processes that include the planning phase, the invitation to tender and awarding of the contract, design, construction, commissioning, acceptance, and invoicing of the project. Experience from many projects shows that shortening the duration of the project and compiling binding project documentation make an important contribution towards reducing the economic risk of major investments. Shorter projects do not tie up new capital and personnel for as long.
Maintenance – a major competitive factor
Efficient maintenance is an important competitive factor for the plant operator. A particular maintenance measure is efficient if it takes place at an optimum point in time, namely at a defined interval to the occurrence of any possible damage. Maintenance measures not only restore the plant to its original state, but also improve it to the necessary technical level.
Mechanical and electrical workshops form the backbone for maintenance work. Depending on the task, the workshops maintain a machine park – for production and repair activities – that is optimised for a company’s actual plant technology. The workshops have a particularly detailed knowledge of process and plant technology. This enables them to carry out maintenance orders reliably and at a reasonable price. They can also react very quickly in the case of disruption, contributing towards a considerable reduction in downtimes and the resultant loss of production.
Automation technology in steel production
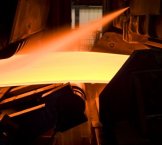
Most production processes in the steel industry are not continuous and have short reaction times. Fluctuating starting conditions and changing capacity utilisations are constraints that considerably complicate automation. There is also a variety of very rapid and dynamic processes in rolling and forming plants with almost linear transfer characteristics, for which a high level of automation has been achieved. The most important developments of recent years have taken place on the process control level. Modern process control systems are digital decentralised process automation systems. In addition to the basic functions of measurement, control, regulation, operation and observation, decentralised systems offer improved automation functions, e.g. the automatic formulation procedure or process models.
Observing processes – planning maintenance
Production plants in the steel industry are frequently operated at the limits of their capacities. This could result in multiple malfunctions. It is therefore necessary to determine, as accurately as possible, the state of the plants and particularly that of critical components – in order to permit the information to be exploited in the maintenance strategy. Condition monitoring systems offer a potential solution here.
Fluid technology in the hydraulics
Fluid technology is exploited in hydraulic systems. They started being used in heavy industries during the 1950s and developed into the motor of drive and automation technology in mobile machines and industrial applications. Steel industry plants without hydraulics are simply inconceivable now. Hydraulic drives and control systems are found throughout the entire production process, from the coking plant to further processing, as well as in the machine and plants of auxiliary operations.
Reducing friction – conserving resources
Tribology (the science of interacting surfaces) examines the dependencies of friction, wear and lubrication. Friction, and thus wear, takes place at numerous machine elements such as bearings, guides, gears, motors, etc. Reducing friction through suitable lubricants results in longer service lives for components, lower energy consumption for movements, and thus cost savings. The German steel industry purchases about 15,000 tonnes of oils and greases per year, costing approx. 18 m. euros. The products purchased are subject to comprehensive testing and laboratory examinations in order to ensure that defined quality demands are met. Current developments aim to optimise the entire tribosystem and produce new improved lubricants. General trends include increased operating temperatures, reduced friction, longer service lives and lower costs.
Cranes: the driving force of the steel industry
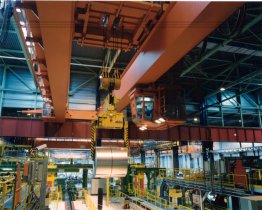
The most varied of cranes can be found in all areas of steel production, starting from simple loading cranes to casting cranes in the steelworks capable of moving loads of up to about 600 tonnes and meeting maximum safety and reliability demands. The load uptake equipment differs depending on the site of use and transport task. Typical systems for the steel industry include: claws (e.g. for slabs, billets), hooks (for coils), magnets and grippers. Very many cranes used in the steel industry originate from the 1960s and 1970s and have therefore undergone several modernisations during their service lives
Maximising resources and benefits through plant management
The maintenance and further development of plants for steel production, forming and further processing make a major contribution towards value creation in the companies of the steel industry. Plant technology controls the available resources in a complex environment and follows the principles of resource conservation and the maximisation of benefits. The provision of process, plant and product data considerably expands the range of activities in plant technology which, however, will continue to find itself in the classic conflict – between demands for increased quality and plant availability and the growing costs pressure. Plant technology thus faces the following challenges:
- consistent use of new technologies and techniques,
- further qualification of personnel,
- organisational changes,
- increasing complexity of the plants currently in use,
- increased demands regarding plant availability,
- reduced costs and improved quality,
- improved maintenance processes.