Kohlenstoffbasierte Stahlerzeugung
Kohlenstoffbasierte Stahlerzeugung
Roheisen- und Rohstahlerzeugung
Die Stahlerzeugung wird durch zwei wesentliche Verfahrensrouten gekennzeichnet: durch den Weg vom „Eisenerz zum Stahl“ und durch den Weg vom „Schrott zum Stahl“. Bei der eisenerzbasierten Route wird meistens aus oxydischen Eisenerzen im Hochofen, seltener in Schmelz-reduktionsanlagen Roheisen erzeugt, das im Sauerstoffkonverter zu Rohstahl verarbeitet wird. In Direktreduktionsanlagen aus Eisenerzen hergestellter Eisenschwamm (Direct Reduced Iron (DRI); Hot Briquetted Iron (HBI)) wird im Elektrolichtbogenofen zu Rohstahl umgewandelt. Bei der schrottbasierten Route wird durch Recyceln von Stahlschrott im Elektrolichtbogenofen Rohstahl hergestellt.
Die Höhe der Stahlerzeugung und der Stahlverwendung eines Landes bzw. einer Region hängt von der Entwicklung der Bevölkerung sowie vom technischen und wirtschaftlichen Entwicklungsstand ab. Die Weltrohstahlerzeugung stieg von 40 Mio. t im Jahr 1900 auf 1,8 Mrd. t im Jahr 2018 an. Deutschland steht mit 42,4 Mio. t Jahreserzeugung in der Rangliste an siebter Stelle, China ist mit 927 Mio. t der größte Stahlerzeuger der Welt. Stahl ist und bleibt auch in diesem Jahrhundert der Werkstoff Nr. 1.
Roheisenerzeugung im Hochofen
Bei der Verfahrensroute über den Hochofen wird zunächst aus Eisenerzen, Zuschlägen sowie Koks und Reduktionsmitteln wie Kohle, Öl oder Gas flüssiges Roheisen gewonnen, das im nachgeschalteten Sauerstoff-Konverterstahlwerk zu Rohstahl umgewandelt wird.
Ein Hochofen ist ein schachtförmiges Aggregat, das nach dem Gegenstromprinzip arbeitet. Die grobkörnigen Einsatzstoffe, Koks und Möller (Eisenerz + Zuschläge), werden von oben über die Gicht chargiert, während das Reduktionsgas von unten der absinkenden Schüttung entgegenströmt.
Vorbereitung der Hochofeneinsatzstoffe
Um die Durchgasung der Schüttsäule im Hochofen zu gewährleisten, ist die Vorbereitung der Einsatzstoffe wichtig. Eisenerze werden in Form von Stückerzen, Sinter und Pellets eingesetzt. Stückerze sind bei den Eisenerzgruben natürlich abgebaute verwertbare Erze größerer Körnung. Bei den Eisenerzgruben fallen allerdings durch Aufbereitungs- und Anreichungsprozesse zur Anhebung des Eisengehaltes zunehmend sehr feinkörnige Erze an, die stückig gemacht werden müssen. Dies erfolgt durch Pelletieren und Sintern.
Beim Pelletieren werden Feinsterze (Pelletfeed) und Konzentrate mit Korngrößen von weit unter 1 mm zu Kügelchen von etwa 10 bis 15 mm Durchmesser geformt. Zu diesem Zweck wird die Erzmischung angefeuchtet und mit einem Bindemittel versehen. In Drehtrommeln oder auf Drehtellern werden dann die „Grünpellets“ geformt. Diese Grünpellets werden getrocknet und bei Temperaturen von mehr als 1000 °C gebrannt. Dies kann im Schachtofen, Drehrohrofen oder auf einem Wanderrost geschehen. Pelletieranlagen stehen in der Regel bei den Eisenerzproduzenten.
Die Sinterung (Sintern = Zusammenbacken) wird auf Sinteranlagen durchgeführt, die Bandbreiten von mehr als 4 m und Bandlängen von über 100 m aufweisen können. Für die Sinterung wird eine Mischung aus Feinerzen zusammen mit Koksgrus, Zuschlägen, Kreislaufmaterialien und Rückgut auf einen umlaufenden Rost, das Sinterband, gegeben und der in der Oberfläche enthaltene Koksgrus mit Gasflammen in einem Ofen gezündet. Ein Gas- bzw. Luftstrom wird von oben nach unten durch die Mischung gesaugt. Eine Wärmefront durchläuft so über die Bandlänge die ca. 500 mm dicke Schicht und bewirkt ein Zusammenbacken der Mischung zu groben Erzklumpen. Sinteranlagen stehen in der Nähe der Hochöfen auf dem Gelände der Stahlproduzenten.
Alle Eisenerze enthalten Sauerstoff, der im Hochofenprozess durch Reduktion entfernt werden muss. Dazu wird Kohlenstoff eingesetzt. Der wichtigste Kohlenstoffträger ist der Hochofenkoks, der heute in modernen, umweltfreundlichen Kokereien hergestellt wird. Unter Verkoken wird das Erhitzen von Kohle in Kokskammern unter Luftabschluss verstanden. Dabei werden die flüchtigen Bestandteile wie Koksofengas, Teer, Benzol, Schwefelwasserstoff, Ammoniak ausgetrieben, aufgefangen und anderer Verwendung zugeführt.
Hochofenprozess
Zur Reduktionsgaserzeugung wird im unteren Teil des Hochofens 1200 °C heiße Luft eingeblasen. Der in diesem Bereich vorliegende Kokskohlenstoff vergast mit dem Sauerstoffgehalt der Luft zum Reduktionsgas Kohlenmonoxid und erzeugt dabei Temperaturen von bis zu 2200 °C. Das entstehende Gas steigt nach oben, bindet im Eisen enthaltenen Sauerstoff und erreicht damit die Reduktion der Erze. Die aufsteigenden Gase erwärmen die darüber liegende Beschickung. Die Begleitelemente der Einsatzstoffe bilden eine flüssige Schlacke und können so abgetrennt werden. Roheisen und Schlacke sammeln sich im unteren Bereich des Hochofens und verlassen den Hochofen über ein zu öffnendes Stichloch im unteren Bereich mit einer Temperatur von rund 1500 °C. Über ein feuerfest ausgekleidetes Rinnensystem werden Roheisen und Schlacke getrennt und den Roheisentorpedopfannen und Schlackenpfannen zugeführt.
Aus Gründen der Optimierung des Prozesses und der Senkung der Herstellungskosten werden als Koksersatz auch andere Kohlenstoffsträger, wie Kohle, Öl, Gas oder aufbereitete Altkunststoffe, in den Hochofen eingeblasen. Sein Betrieb ohne Koks ist allerdings nicht möglich. Der Koks behält in den Bereichen des Hochofens, in denen die Erze weich werden und schmelzen, seine feste Struktur bei. Er garantiert damit die Durchgasung und dient als Stützgerüst für die obere feste Beschickungssäule.
Große Hochöfen weisen Gestelldurchmesser von rund 15 m auf und haben ein Gesamtvolumen von rund 6000 Kubikmeter. Sie produzieren rund 13000 Tonnen Roheisen pro Tag oder mehr als 4 Millionen Tonnen Roheisen pro Jahr. Dafür müssen täglich große Materialströme bewegt und zugeführt werden, z.B.: 20800 Tonnen Eisenerze, 4300 Tonnen Koks, 1900 Tonnen Einblaskohle, 12 Millionen Kubikmeter Luft, die in Winderhitzern auf über 1200 °Celsius erhitzt werden. Weiterhin fallen täglich 3600 Tonnen Schlacke an, die überwiegend als Baustoff in der Zementindustrie oder im Straßenbau verwertet wird, sowie 18 Millionen Kubikmeter Hochofengas, das nach Reinigung energetisch genutzt wird.
Die Lebensdauer eines Hochofens, d.h. die Zeitspanne, bis seine feuerfeste Ausmauerung vollständig erneuert werden muss, beträgt heute 15 bis 20 Jahre.
Eisenerzeugung durch Direkt- oder Schmelzreduktion
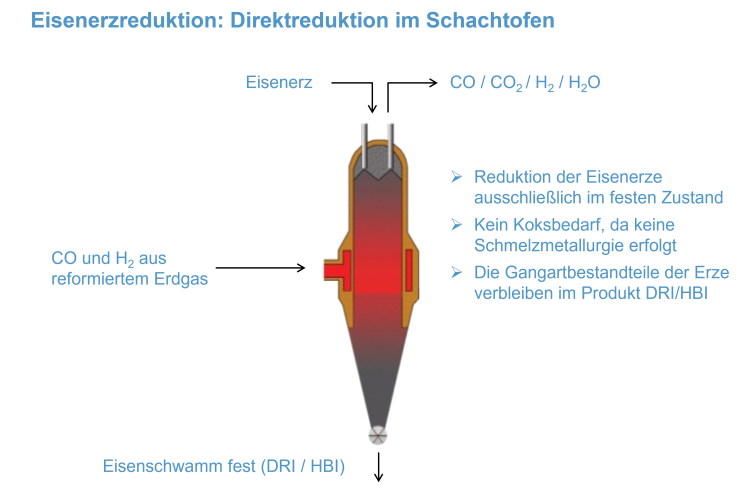
Es sind auch Verfahren entwickelt worden, die Erze unter Umgehung von Koks reduzieren. Diese werden mit den Begriffen Direktreduktion und Schmelzreduktion zusammengefasst.
Bei der Direktreduktion wird kein flüssiges Roheisen erzeugt, da das Verfahren bei niedrigeren Temperaturen arbeitet als der Hochofen. Den Erzen wird lediglich der Sauerstoff entzogen, und die Gangartbestandteile der Erze verbleiben im so genannten Eisenschwamm (DRI – Direct Reduced Iron; HBI – Hot Briquetted Iron). Die Reduktionsgaserzeugung erfolgt bei den meisten Direktreduktionsverfahren durch Umwandlung von Erdgas in Wasserstoff und Kohlenmonoxid. Der Eisenschwamm wird im Wesentlichen im Elektrolichtbogenofen eingesetzt.
Bei der Schmelzreduktion wird zweistufig gearbeitet. Zunächst werden die Erze zu Eisenschwamm reduziert und dieser anschließend unter Einsatz von Kohle und Sauerstoff zu einem hochofenähnlichen Roheisen umgewandelt. Von den Schmelzreduktionsprozessen sind bisher lediglich die Verfahren Corex und Finex in der betrieblichen Anwendung.
Beide Verfahrensweisen sind von der Wirtschaftlichkeit her auf bestimmte Regionen und Anlagenkonfigurationen begrenzt und können die Produktionsleistungen eines großen Hochofens nicht erreichen.
Stahlerzeugung
Das Roheisen enthält störende Begleitelemente wie Kohlenstoff, Silicium, Schwefel und Phosphor. Diese Bestandteile werden im so genannten Oxygenstahlkonverter durch Einblasen von Sauerstoff entfernt. Dabei werden die Verunreinigungen oxidiert und schwimmen als Schlacke auf dem Metallbad auf.
Der Blasprozess für 300 t Material dauert ca. 20 Minuten und verläuft unter starker Wärmeentwicklung. Zur Kühlung wird dem Konverter daher bis zu 25 % Schrott zugesetzt. Hinzugefügter Kalk unterstützt die Schlackenbildung. Nach Abschluss des Blasprozesses werden Schlacke und Rohstahl beim Abstechen des Konverters getrennt. Dazu wird der Konverter in die Abstichposition geneigt. Die Schmelze wird über das Abstichloch in eine Stahlpfanne geleitet. Die Schlacke wird im Konverter zurückgehalten und anschließend der Weiterverwertung zugeführt.
Die größten Konvertergefäße fassen heute bis zu 400 t Rohstahl. Neben dem reinen Sauerstoff-Aufblasprozesses (LD-Konverter) werden heute durch den Boden blasende Konverter (OBM-Konverter) oder auch kombiniert von oben und durch den Boden blasende Konverter (K-OBM-Konverter) eingesetzt. Zur Verbesserung der Durchmischung im Konvertergefäß kann mit Inertgasen durch den Boden oder die Seitenwände während des Blasprozesses gespült werden.
Rohstahlerzeugung im Elektrolichtbogenofen
Stähle auf der Basis von Schrott werden im Elektrolichtbogenofen erschmolzen. Der Lichtbogen überführt die elektrische Energie mit sehr gutem Wirkungsgrad und hoher Energiedichte in Schmelzwärme. Neben Schrott können auch Eisenschwamm (DRI oder HBI) sowie flüssiges oder festes Roheisen chargiert werden. Grundsätzlich kann über die Elektrolichtbogenofenroute, je nach Qualität des metallischen Einsatzes, jede Stahlsorte erzeugt werden.
Die wesentlichen Bauelemente des Lichtbogenofens sind das Ofengefäß mit Absticherker und Arbeitsöffnung, der abnehmbare Deckel mit den Graphitelektroden und die Kippvorrichtung. Das Ofengefäß ist feuerfest ausgemauert. Zum Befüllen des Ofens wird der Deckel angehoben und zur Seite geschwenkt. Der Schrott wird mit Körben über den Ofen gefahren und in den Ofen gefüllt. Anschließend wird der Deckel erneut aufgesetzt, die Elektroden werden heruntergefahren und der Lichtbogen auf dem kalten Schrott gezündet. Bei dem Einschmelzprozess entstehen im Lichtbogen Temperaturen bis zu 3500 °C, in der Stahlschmelze bis zu 1800 °C. Zusätzliches Einblasen von Sauerstoff oder anderer Brennstoff-Gasgemische beschleunigt den Schmelzprozess. Sind die gewünschte chemische Zusammensetzung und Temperatur des Stahles erreicht, wird der Ofen durch Kippen in die Stahlpfanne entleert.
Unterschieden wird zwischen Drehstrom- und Gleichstromlichtbogenofen. Allgemein hat der Drehstromofen einen deutlich höheren Verbreitungsgrad als der Gleichstromofen. Letzterer hat Vorteile hinsichtlich geringerer Netzrückwirkungen, geringerer Geräuschemissionen und des geringeren Elektrodenabbrands. Die Nachteile bestehen in der erforderlichen Sumpffahrweise und der aufwendigeren Elektrodenpflege.
Hinsichtlich Größe und Leistungsfähigkeit ist die Bandbreite der eingesetzten Öfen enorm. Die kleinsten Elektrolichtbogenöfen mit Abstichgewichten von 5 Tonnen Rohstahl arbeiten in der Gießereiindustrie. Die weltweit größten Elektrolichtbogenöfen aus der Stahlindustrie verfügen über Abstichgewichte von 300 Tonnen bei Jahresproduktionsmengen von 2,6 bis 2,8 Millionen Tonnen Rohstahl im Jahr. Dabei wird die Produktionskapazität mittelgroßer Blasstahlwerke erreicht. Je nach Größe und Konfiguration des Ofens können heute Energieverbräuche von 350 Kilowattstunden je Tonne Rohstahl bei tap-to-tap-Zeiten von 40 Minuten und Elektrodenverbräuchen von 1,1 Kilogramm je Rohstahl erzielt werden.
Sekundärmetallurgie: Feintuning des Stahls
Die hohen Anforderungen an die modernen Stähle erfordern eine Nachbehandlung der in der Stahlpfanne bereitgestellten Schmelzen. Dies gilt sowohl für die Hochofen-Konverter-Route als auch für die Elektrolichtbogenofen-Route. Die wesentlichen Ziele dieser sekundärmetallurgischen Behandlung sind die Einstellung der chemischen Zusammensetzung des fertigen Stahls, der Gießtemperatur und des Reinheitsniveaus. Dabei sind im Einzelnen folgende Aufgaben zu unterscheiden:
- Legieren,
- Homogenisieren der Schmelze,
- Tief-Entkohlen,
- Entschwefeln,
- Entgasen,
- Desoxidieren und
- Abscheiden bzw. Konditionieren nichtmetallischer Einschlüsse.
Wie die Werkstoffspektren sind die metallurgischen Aufgaben für die Blasstahlwerke und die Elektrostahlwerke ähnlich vielfältig, so dass vergleichbar komplexe sekundärmetallurgische Behandlungswege entstehen.
Sekundärmetallurgische Prozessrouten: Behandlungsmöglichkeiten
Ein allgemeiner Trend der sekundärmetallurgischen Behandlung ist die Steigerung der Stahlqualitäten bei zunehmender Flexibilität der metallurgischen Anlagen. Daher bleibt die weitere Verbesserung der Stahlwerkslogistik eine permanente Aufgabe. Die Anzahl der sekundärmetallurgischen Aggregate und Ausrüstungen in den Stahlwerken steigt weiter an. Gleichzeitig nimmt die Funktionalität der Aggregate zu, um so den Anforderungen an die neuen Qualitäten und an die Flexibilität der Werke gerecht zu werden.
Stahl im Fluss: Vergießen des Stahls
Zur späteren Weiterverarbeitung wird der in der Sekundärmetallurgie erzeugte noch flüssige Stahl vergossen und erstarrt. Rund 96 Prozent des flüssigen Stahls wird in Deutschland heute in Stranggussverfahren verarbeitet, weltweit beträgt der Stranggussanteil ca. 93 Prozent. Der Rest wird in sogenannten Blöcken vergossen. Der Gießbetrieb liegt im Materialfluss eines Hüttenwerkes hinter dem Stahlwerk und vor den Weiterverarbeitungsbetrieben, den Walz- bzw. Schmiedewerken.
Beim Stranggießen gelangt der flüssige Stahl aus der Gießpfanne über den Gießverteiler in eine wassergekühlte Durchlaufkokille. Die Form der Kokille bestimmt das Format des Stranges. Wegen seines flüssigen Kerns muss der Strang bis zur Durcherstarrung mit Wasser bzw. Wasser-Luftgemischen gekühlt werden. Der Strang wird dabei durch Rollen abgestützt, um ein Aufbrechen der Strangschale zu vermeiden. Die intensive Kühlung bewirkt ein gleichmäßiges Erstarrungsgefüge mit günstigen technologischen Eigenschaften. Nach der Erstarrung kann der Strang durch Schneidbrenner oder Scheren auf gewünschte Längen zerteilt werden.
Beim Blockgießen werden die als Standkokillen bezeichneten Gießformen entweder über ein feuerfestes Kanalsystem in der Regel von unten (Unterguss), oder in seltenen Fällen von oben (Oberguss) mit flüssigem Stahl gefüllt. Der Stahl erstarrt in den Kokillen. Die Kokille wird nach der Erstarrung des Stahls per Kran gestrippt, d.h. vom erstarrten Block getrennt und kann dann im Walz- oder Schmiedewerk weiterverarbeitet werden. Gängige Formate sind Rund- oder Vierkant- oder Polygonalblöcke. Die Blockgewichte können zwischen 50 kg und 600 t betragen.
Verarbeitet werden im Blockguss vor allem Spezialstähle mit kleinen Mengen, Halbzeuge für Profile mit großen Querschnitten für die Schmiedeindustrie, Brammenblöcke für dicke Blecke, Wälzlagerstähle und Werkzeugstähle, Vollaustenite sowie Stahlsorten, die im Strangguss nicht ausreichend beherrscht werden.
Die Stranggießtechnik ist gegenüber dem Blockguss auf die Massenproduktion abgestimmt. Durch die Möglichkeit zum Sequenzgießen (Vergießen mehrerer Pfannen nacheinander durch einen Kokillensatz) wird eine maximale Anlagenauslastung erreicht.Kon