Oberflächenveredelung
Oberflächenveredelung
Oberflächenveredelung von Bandstahl
Die Veredelung von Stahloberflächen dient dem Korrosionsschutz und der Herstellung dekorativer Oberflächen. Dies geschieht durch Beschichtung mit metallischen oder organischen Überzügen. Oberflächenveredelte Stahlprodukte werden als Bänder, Bleche und Profile vor allem in der Automobil-, der Bau-, der Hausgeräte- und der Verpackungsindustrie eingesetzt.
Schmelztauchbeschichtung
Schmelztauchbeschichtungslinien werden metallische Überzüge auf das kaltgewalzte Feinblech aufgebracht. Erzeugt werden folgende Überzüge:
- Zink (Z)
- Zink-Eisen (ZF)
- Zink-Magnesium-Aluminium (ZM)
- Zink-Aluminium (ZA), Galfan
- Aluminium Zink (AZ), Galvalume
- Aluminium-Silizium (AS)
Bandveredelungsanlagen werden generell kontinuierlich betrieben: Im Einlauf wird durch Verschweißen einzelner Bänder ein Endlosband erzeugt, das nach der Beschichtung im Auslauf wieder zerteilt und zu Coils aufgewickelt wird. Das Band kommt walzhart, d. h. direkt vom Kaltwalzen in die Anlage. Es wird in einem Durchlaufofen rekristallisierend geglüht sowie unter Schutzgas durch einen Kessel (Kesselinhalte zwischen 200 und 350 t sind üblich) mit dem flüssigen Beschichtungsmetall (beim Feuerverzinken ca. 450 °C) gezogen. Die gewünschte Schichtdicke, die üblicherweise zwischen 5 und 50 µm beträgt, wird mittels Abblasen mit Luft oder Stickstoff durch sogenannte Abstreifdüsen eingestellt. Nach dem Abkühlen des beschichteten Bandes wird es nachgewalzt und kann chemisch nachbehandelt (passiviert oder phosphatiert) werden. Durch online-Oberflächeninspektion und online-Einölen kann das veredelte Band bereits direkt in der Beschichtungsanlage zur Verpackung und für den Versand an den Kunden vorbereitet werden.
Feuerverzinktes Band wird in Dicken von 0,35 bis 3,00 Millimeter und Breiten bis zu 2.060 Millimeter gefertigt. Die maximalen Bandgeschwindigkeiten einer Schmelztauchveredelungsanlage liegen bei ca. 150 bis 220 Meter je Minute. Die Jahreskapazität einer solchen Anlage liegt je nach Auslegung bei ca. 350.000 bis 500.000 Tonnen.
Die Technologie der Oberflächenveredelung entwickelt sich ständig fort. Neue Anlagen
- verfügen über Vertikalöfen mit präzisen Glühzyklen zur Erzeugung beschichteter Feinbleche auch höher- und höchstfester Stahlsorten.
- sind mit Wechsel- oder Standby-Kesselsystemen ausgerüstet, um verschiedene Beschichtungsvarianten bei schnellen Produktwechseln herstellen zu können.
- setzen die Elektromagnetische Stabilisierung des Bandes nach Verlassen des Schmelzbades ein: Die Zinkschichtdicke kann optimal eingestellt werden, da der Abstand zwischen den Abstreifdüsen und dem durchlaufenden Band mit dem noch flüssigen Überzug über die Bandbreite konstant gehalten wird.
- binden das Düsenabstreifsystem zur Regelung der Schichtauflagen in einen Regelkreis ein. Für diese Regelkreise wird modernste Regelungstechnik mit dem Einsatz von Neuronalen Systemen zur Schichtdickenregelung kombiniert.
- wenden zunehmend prozessübergreifend Automatische Oberflächeninspektion an.
Elektrolytische Verzinkung
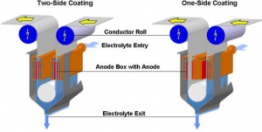
Beim elektrolytischen Verzinken wird durch elektrochemische Abscheidung eine metallische feinkristalline Zinkschicht auf der Bandoberfläche erzeugt. Die mit diesem Verfahren erzielten Schichtdicken liegen üblicherweise zwischen 2,5 und 10 Mikrometer und sind damit wesentlich geringer als beim Feuerverzinken. Im Unterschied zum Schmelztauchveredeln wird hier geglühtes und dressiertes, das heißt nachgewalztes Feinblech eingesetzt, dessen Gefüge keiner weiteren Beeinflussung unterliegt, da das elektrolytische Verzinken bei Raumtemperatur erfolgt.
Nach dem Erzeugen des Endlosbandes im Einlauf wird das Band durch alkalisches Reinigen und Beizen vorbehandelt. Die Beschichtung erfolgt in mehreren Zellen vorzugsweise aus sulfatsauren Elektrolyten. Während frühere Anlagen noch mit löslichen Anoden ausgerüstet waren, sind heutige Anlagen mit unlöslichen (horizontalen oder vertikalen) Anoden ausgestattet. In der Nachbehandlung wird das Band überwiegend zur Verbesserung der Schmierungsbedingungen bei der Weiterverarbeitung mit einer Phosphatschicht versehen.
Elektrolytisch verzinktes Band wird in Dicken von 0,4 bis max. 3,0 Millimeter und in Breiten bis zu 1.950 Millimeter gefertigt. Je nach Sortiment können Bandgeschwindigkeiten bis zu 180 Meter in der Minute erreicht werden. Die maximale Kapazität einer elektrolytischen Veredelungsanlage liegt je nach Auslegung und Sortiment bei ca. 200.000 bis 360.000 Tonnen pro Jahr.
Elektrolytische Verzinnung
Durch das Verzinnen wird das Feinstblech vor Korrosion geschützt und erhält gleichzeitig seinen typischen Glanz. Als Produkt entsteht Weißblech. Bevor die Feinstblechrollen durch die Verzinnungsanlage laufen, werden sie zu einem endlosen Band zusammengeschweißt. Nach einer Reinigung mit einer elektrolytischen alkalischen Behandlung, einer Beize und einer Spüle, gelangt das Band in den Elektrolyten, wo Zinn durch unterschiedliche Stromstärke in gewünschter Schichtdicke aufgetragen wird. Die Oberfläche erhält ihr typisch glänzendes Aussehen, indem sie danach kurzzeitig über den Zinnschmelzpunkt von 232° C erwärmt und anschließend im Wasserbad wieder abgeschreckt wird.
Das so erzeugte Weißblech gelangt entweder direkt als Coil oder zugeschnitten bzw. gespalten zur Weiterverarbeitung. Als Verpackungsmaterial in der Nahrungs- und Genussmittelindustrie findet verzinntes Weißblech breite Anwendung.
Verzinntes Weißblech wird in Dicken bis zu 0,49 Millimeter gefertigt. Elektrolytische Verzinnungsanlagen erreichen Bandgeschwindigkeiten von max. 600 bis 650 Meter je Minute und verfügen über Jahreskapazitäten von bis zu 390.000 Tonnen.
Bandbeschichtung
Bandbeschichtetes Feinblech ist ein Verbundwerkstoff aus unbeschichtetem oder schmelztauch- oder elektrolytisch veredeltem Feinblech und einer organischen Beschichtung , zum Beispiel in Form vonLack oder Folie). Die besonderen Merkmale sind Korrosionsbeständigkeit, Umformbarkeit und dekoratives Aussehen.
Das Vormaterial (Feinblech in Coils) wird gereinigt und chemisch vorbehandelt. Organische Beschichtungsstoffe werden durch einen so genannten Coater aufgetragen und anschließend in einem Schwebeofen getrocknet oder vernetzt. Eine Beschichtung mit Kunststofffolien durch Laminieren ist eine weitere Möglichkeit.
Organisch beschichtetes Band wird in Dicken von 0,40 bis ca. 2,0 Millimeter und Breiten bis max. 1.850 Millimeter hergestellt. Je nach Beschichtungsstoff werden Schichtdicken zwischen 3 und 200 Mikrometer eingestellt.
Die Anlagen zur organischen Beschichtung können Anlagengeschwindigkeiten bis zu 150 Meter je Minute erreichen und verfügen je nach Produkt-Mix über Kapazitäten bis zu 220.000 Tonnen pro Jahr.