Wasserstoffbasierte Stahlerzeugung
Wasserstoffbasierte Stahlerzeugung
Der European Green Deal - Fit for 55
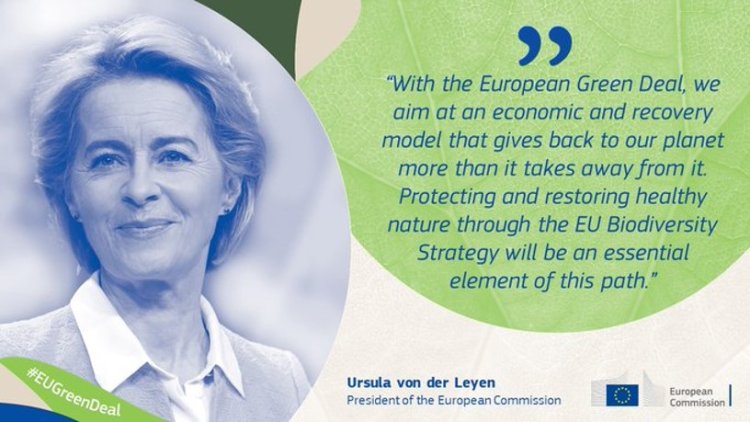
Der Rat der Europäischen Union hat schon 2011 eine Roadmap zum Erreichen einer konkurrenzfähigen „low-carbon economy“ in Europa bis 2050 beschlossen. Daraus geht hervor, dass die europäische Industrie ihre CO2-Emissionen bis zum Jahr 2050 im Vergleich zu 1990 um 80 bis 95 % absolut verringern muss. Am 28. November 2018 hat die EUKommission im Lichte des UN-Klimaabkommens von Paris eine langfristige strategische Vision für eine klimaneutrale Wirtschaft für 2050 sowie am 11. Dezember 2019 mit dem Green Deal das Ziel veröffentlicht, die Europäische Union bis 2050 zum ersten klimaneutralen Kontinent zu machen und dazu einen Aktionsplan vorgelegt. EU-Rat, Europaparlament und EU-Kommission haben am 21. April 2021 im Rahmen des Trilogs eine vorläufige Einigung verkündet, wonach im Rahmen des Europäischen Klimaschutzgesetzes das Klimaziel für 2030 auf eine Treibhausgasminderung um mindestens 55 % gegenüber 1990 angehoben werden soll. Die Erreichung des 55%-Ziels soll durch ein europäisches „Fit for 55“-Gesetzespaket mit einer Revision zahlreicher energie- und klimabezogener EU-Richtlinien umgesetzt werden. Die Stahlindustrie teilt das Ziel, bis 2050 Treibhausgasneutralität zu erreichen, und möchte bereits bis 2030 substanzielle CO2-Einsparungen auf den Weg bringen.
CO2-Emissionen der Verfahren zur Stahlerzeugung
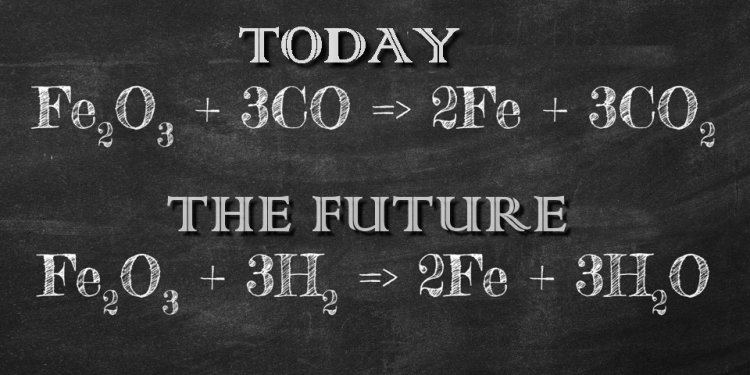
Der größte Anteil der CO2-Emissionen bei der Stahlerzeugung entsteht bei der Reduktion der Eisenerze. Für die Reduktion der Eisenerze, das heißt für den Abbau des Sauerstoffes, ist ein gasförmiges Reduktionsmittel erforderlich. Die einzig möglichen gasförmigen Reduktionsmittel sind Kohlenstoffmonoxid (CO) und Wasserstoff (H2). Die thermodynamische Voraussetzung für das Ablaufen der Eisenerzreduktion ist, dass durch das Einstellen eines geeigneten Kohlenstoffmonoxid- zu Kohlenstoffdioxid- oder Wasserstoff- zu Wasser-Verhältnisses der Sauerstoffpartialdruck des Reduktionsmittels kleiner ist als der Dissoziationssauerstoffdruck des Eisenoxids, also ein Potentialgefälle für den Ablauf der Reaktion vorliegt. Bei der Reduktion mit CO, die exotherm ist, entsteht zwangsläufig das unerwünschte
Treibhausgas CO2. Bei der Reduktion mit H2, die endotherm ist, entsteht H2O, in der Regel in Form von Dampf.
Direktreduktion im Schachtofen
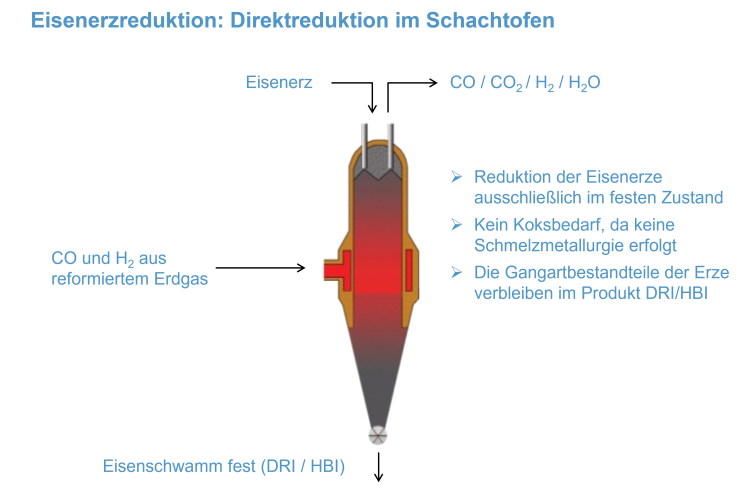
Bei der Direktreduktion von Eisenerzen wird in der betrieblichen Praxis schon seit Anfang der 1970er Jahre wasserstoffreiches Erdgas als Reduktionsmittel zur Reduktion der Eisenerze eingesetzt. Dabei wird zum Beispiel unter Einsatz eines Schachtofens fester Eisenschwamm, international als DRI (Direct Reduced Iron) oder in brikettierter Form als HBI (Hot Briquetted Iron) bezeichnet, erzeugt. Das wesentliche Ziel bei der Entwicklung von Direktreduktionsverfahren bestand darin, unter Vermeidung des Einsatzes von Koks, wie er für den Hochofen erforderlich ist, Eisenerze zu reduzieren.
Reduktionsgas (CO und H2) aus reformiertem Erdgas wird in den unteren Teil der Reduktionszone des Direktreduktionsschachtes eingeblasen. Dem DRI wird zwar weitgehend der Sauerstoff der „stückigen“ Eisenerze (Pellets und Stückerze) entzogen, aber es fällt im festen Zustand an und enthält noch die Gangartbestandteile der Eisenerze. Eine Schmelz- und Schlackenmetallurgie findet nicht statt. Die Weiterverarbeitung des DRI zu Rohstahl mit Schmelzen und Schlackenmetallurgie erfolgt im nachgeschalteten Elektrolichtbogenofen. Die CO2-Emission dieser Route liegt beim Einsatz von Erdgas bei 993 kg/t Rohstahl. Bei dieser Route werden keine energetisch verwendbaren Prozessgase erzeugt. Der gesamte Bedarf an elektrischer Energie auch für alle nachgeschalteten Anlagen muss durch Fremdbezug gedeckt werden.
Wasserstoff als Reduktionsmittel
Die Schwerpunkte bei der Säule CDA (Carbon Direct Avoidance) liegen beim Einsatz von CO2-freier elektrischer Energie und CO2-freiem, grünem Wasserstoff bei der Stahlerzeugung und hierbei insbesondere bei der eisenerzbasierten Direktreduktion und dem Einschmelzen des dabei erzeugten DRI zur Stahlerzeugung im Elektrolichtbogenofen. Bei der DRI-Erzeugung mit Wasserstoff sollen nach derzeitiger Planung überwiegend Schachtöfen zum Einsatz kommen. In solchen Direktreduktions-Schachtofenanlagen werden im Wesentlichen Eisenerzpellets durch Reformieren von Erdgas unter Bildung der Reduktionsmittel CO und H2 im „trockenen“ Zustand ohne Schmelzmetallurgie reduziert, d. h. vom Sauerstoff befreit. Es findet keine Erzeugung eines flüssigen Eisens und keine Schlackenmetallurgie statt; es wird daher auch kein Koks wie beim Hochofen benötigt. Das erzeugte DRI enthält allerdings noch sämtliche Gangartbestandteile (Gesteinsanteile) der Eisenerze. Eine im Vergleich zum Konverter „eingeschränkte“ Schlackenmetallurgie erfolgt in der nachgeschalteten Stahlerzeugungsstufe Elektrolichtbogenofen. Die Schlackenmenge ist beim Elektrolichtbogenofen verfahrenstechnisch begrenzt. Um die Schlackenmenge möglichst niedrig zu halten, werden deshalb bei der DR-Anlage sogenannte DR-Pellets, die im Vergleich zu Hochofenpellets deutlich geringere Gangartbestandteile und somit höhere Fe-Gehalte haben, eingesetzt. Die bei der DR-Pelletherstellung eingesetzten Feinerze müssen dementsprechend intensiver aufbereitet werden.
Rohstahlerzeugung im Elektrolichtbogenofen
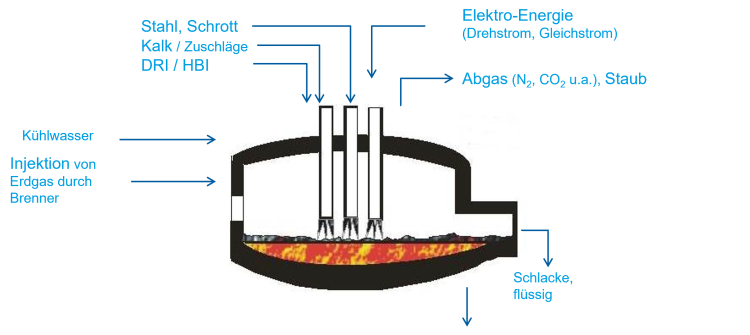
Die wesentlichen Bauelemente des Lichtbogenofens sind das Ofengefäß mit Absticherker und Arbeitsöffnung, der abnehmbare Deckel mit den Graphitelektroden und die Kippvorrichtung. Das Ofengefäß ist feuerfest ausgemauert. Zum Befüllen des Ofens wird der Deckel angehoben und zur Seite geschwenkt. Der Schrott wird mit Körben über den Ofen gefahren und in den Ofen gefüllt. Anschließend wird der Deckel erneut aufgesetzt, die Elektroden werden heruntergefahren und der Lichtbogen auf dem kalten Schrott gezündet. Bei dem Einschmelzprozess entstehen im Lichtbogen Temperaturen bis zu 3500 °C, in der Stahlschmelze bis zu 1800 °C. Zusätzliches Einblasen von Sauerstoff oder anderer Brennstoff-Gasgemische beschleunigt den Schmelzprozess. Sind die gewünschte chemische Zusammensetzung und Temperatur des Stahles erreicht, wird der Ofen durch Kippen in die Stahlpfanne entleert.
Unterschieden wird zwischen Drehstrom- und Gleichstromlichtbogenofen. Allgemein hat der Drehstromofen einen deutlich höheren Verbreitungsgrad als der Gleichstromofen. Letzterer hat Vorteile hinsichtlich geringerer Netzrückwirkungen, geringerer Geräuschemissionen und des geringeren Elektrodenabbrands. Die Nachteile bestehen in der erforderlichen Sumpffahrweise und der aufwendigeren Elektrodenpflege.
Hinsichtlich Größe und Leistungsfähigkeit ist die Bandbreite der eingesetzten Öfen enorm. Die kleinsten Elektrolichtbogenöfen mit Abstichgewichten von 5 Tonnen Rohstahl arbeiten in der Gießereiindustrie. Die weltweit größten Elektrolichtbogenöfen aus der Stahlindustrie verfügen über Abstichgewichte von 300 Tonnen bei Jahresproduktionsmengen von 2,6 bis 2,8 Millionen Tonnen Rohstahl im Jahr. Dabei wird die Produktionskapazität mittelgroßer Blasstahlwerke erreicht. Je nach Größe und Konfiguration des Ofens können heute Energieverbräuche von 350 Kilowattstunden je Tonne Rohstahl bei tap-to-tap-Zeiten von 40 Minuten und Elektrodenverbräuchen von 1,1 Kilogramm je Rohstahl erzielt werden.
Der Elektro-Niederschachtofen
Eine weitere Verfahrensvariante bei der Nutzung der Direktreduktionstechnologie auf Wasserstoffbasis ist das Einschmelzen des DRI in einem Elektroniederschachtofen (SAF - Submerged Arc Furnace oder OSBF - Open Slag Bath Furnace) zu flüssigem Roheisen mit entsprechender Schlackenmetallurgie und die Umwandlung des Roheisens zu Rohstahl im Sauerstoffkonverter. Diese Option ermöglicht es, das vorhandene Oxygenstahlwerk mit seinen metallurgischen Vorteilen weiter zu betreiben und somit die bisher hergestellten Stahlqualitäten auch in Zukunft herstellen zu können. Submerged Arc Furnaces oder Open Slag Bath Furnaces können rund oder rechteckig gebaut werden, die Bauhöhen betragen bis zu 10 m. Die Elektroden tauchen tief in die Beschickung ein, der Wärmeübergang erfolgt durch die Schlacke. Diese Verfahren arbeiten in reduzierender Atmosphäre und eignen sich daher gut zur Reduktion der FeO-Gehalte des DRI und zum Aufkohlen der Schmelze zu Roheisen. Es sind kontinuierlich und gleichmäßig arbeitende Prozesse, wodurch bei der Stromversorgung das typische „Flimmern“ des Elektrolichtbogenofens nicht auftritt.